Surface Coatings
Because changing the basic composition in a glass tank to produce body coloured glass products i
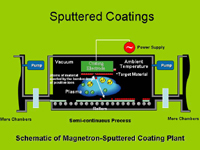
s a lengthy and large scale operation, modified properties are produced from basic clear glass by surface coatings applied during manufacture on-line or subsequently off-line.
OFF-LINE COATINGS
Off-line coatings are those which are applied to individual panes of glass once the glass has been manufactured and cut. The application of coatings, by dipping panes into chemical solutions, drying and firing, or by evaporation of metals on to glass surfaces under conditions of vacuum, has been known for many years, but in the last decade application by magnetron sputtering of materials has come to the forefront. This process is capable of giving a wide range of coatings of different colours, reflectivities and thermal properties.
In magnetron sputtering, the material to be sputtered is made the cathode of an electrical circuit at 500 volts
(Click here to view the image above in a separate window).
Argon gas is introduced into a vacuum chamber, and a glow discharge plasma occurs. Electrons are removed from the argon and leave positively charged ions. These ions are attracted to, and impact with, the target cathode. They have very high momentum and eject atoms of the cathodic material which recondense on the glass below.
Fine tuning enables uniform coatings to be laid on large substrates. Panes 3000 x 2000 mm can be sputter coated at a rate of one every 60 seconds or so. Virtually any non-magnetic metal or alloy can be sputtered. If argon is in the chamber, a metallic coating results; if oxygen or nitrogen, the result is an oxide or a nitride. A large number of designed coatings is available. Light transmission depends on the nature and thickness of coating. Colour depends on coating thickness material and configuration. The product ranges are under continuous development.
ON-LINE COATINGS
On-line modifications are made while the glass is hot and still in the annealing lehr. They may still be considered as basic products, and size and tolerance constraints are similar to those for clear float glass.
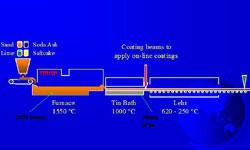
Surface coatings, either for solar control purposes or for reduced emissivity (a property to improve thermal insulation), are called pyrolitic coatings because they are generally applied to the hot glass during its passage through the annealing lehr. They involve the thermal decomposition of gases, liquids or powders sprayed on to the glass to form a metal oxide layer which fuses to the surface.
On-line coatings have advantages of hardness and durability over off-line coatings and are suitable for bending and toughening. They tend to be limited in variety of colour.
(Click here to view the Low E Online Manufacturing Process in a separate window)
DIELECTRIC COATINGS
The range of performances available from the use of metallic coatings is limited because of the thickness of coating which has to be applied. The use of dielectric coatings, which produce interference effects, allows higher light transmission with increased selectivity; the range of colours is also increased.
The maximum sizes of coated glass are dependent on the various facilities, and manufacturers' literature should be consulted.
It is not possible to toughen or bend most off-line coated glass; such work must be carried out before coating. It is possible to combine coatings in double glazed and laminated products.
DICHROIC COATINGS
These are composed of multi-layered coatings which exhibit different colours by reflection and transmission as a function of viewing angle.
MIRROR SILVERING
Mirror silvering is a chemical process depositing a coating of metal, mostly silver, on to the surface of clear glass. This deposit is usually protected by a layer of copper which in turn is protected by a paint backing. The silver gives the mirror its reflective properties. The controlled use of stannic solution can produce decorative 'oil-stain' patterns which can be painted with a coloured transparent varnish.