Air Emissions
The main emissions from a flat glass furnace come from the combustion of fuel and the decomposition of the carbonate and sulphate raw materials. The raw materials are melted at a very high temperature so the process is extremely energy-intensive.
Emissions to air
The most significant pollutants from a glass furnace are: nitrogen oxides formed from the nitrogen and oxygen in the air at high temperature; sulfur oxides from the refining agent (and from oil fuel if that is used); and particulate matter derived from compounds volatilized from the molten glass. Carbon dioxide comes from both the decomposition of carbonates and from combusted fuels.
We are tackling pollutant air emissions with a range of primary and secondary abatement techniques. Primary methods, such as special burners or carefully-chosen raw materials, including more cullet (recycled glass), reduce pollutant formation and can also improve the thermal performance of the furnaces.
Secondary abatement removes the pollutants from the furnace waste gases before they are emitted through the chimney.
Until recently, the furnace emission pollution control plants in operation around NSG Group have all been based on standard technology. This removes the pollutants from the waste gases in three stages: alkali is injected into a scrubber to remove acid gases, the resultant reaction products and particulate emissions are then collected in an electrostatic precipitator, and finally nitrogen oxide is removed using ammonia injected into a selective catalytic reduction unit. However, the latest pollution control plant built by NSG Group uses a novel technique called a catalytic ceramic filter, or CCF.
The system is based on thousands of ceramic filters in a single unit. Alkali is added to the waste gas and the resultant reaction products and primary particles are collected by the filter. The novelty of the process is that the fibers of the filters are coated with a metal catalyst so when the gases pass through the filter structure and ammonia is added to the system nitrogen oxides are also removed. It is expected that CCF technology will become the standard for new furnace pollution control plant throughout NSG group.
Our Lirquen site in Chile has almost completed the implementation of a pollution control plant project. Once completed, the existing plant will be capable of reducing particulate matter, SO2 and NOx.
The peculiarity about NOx reduction - which is specific to the Lirquen plant - is that the reducing agent is 30% urea water solution, instead of the more common water ammonia solution.
Urea solution will be added to the incoming hot raw gases coming off the furnace, before entering the cooling tower. Due to the high raw gas temperature, urea will decompose into ammonia (NH3) in the gas before it is cooled in the downstream cooling tower and the subsequent candle unit.
In here, thanks to catalyst particles embedded onto the ceramic candle surface, NH3 reacts with NOx components, bringing them down to the desired concentration. Thanks to the solid hydrated lime injected into the system, and to the candle filter porous surface, SO2 and particulate matter are also reduced.
Urea solution usage at Lirquen as an alternative to the more common use of ammonia solution, will be the first example of this type of NOx reduction within NSG Group.
NOx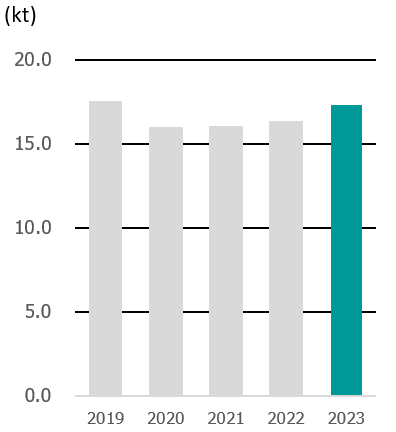
SOx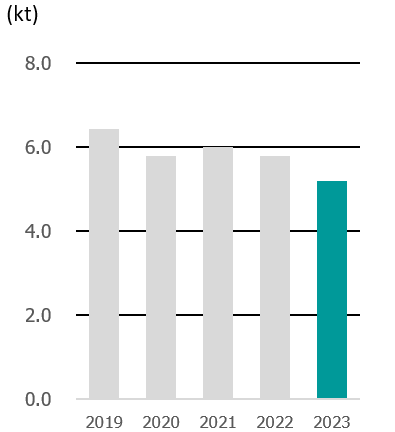
Recycled glass to improve efficiency and reduce emissions
Glass for recycling is a valuable resource. Wherever quality allows, we recycle any glass off-cuts or cullet within our own glass melting lines. Glass from our downstream operations and from our customers represents a potentially useful resource to us. We gain a double benefit from the use of such cullet: its use to make glass reduces the requirement for raw materials and avoids disposing of what would otherwise be a waste material and closes the recycling loop.
Cullet return projects are ongoing to try to minimize the need for virgin raw materials. Landfill is the least favored disposal option.
If glass is produced that cannot be remelted on-site, it is sent, where practicable, for external recycling.